Recognizing the Fundamentals and Applications of Plastic Extrusion in Modern Production
In the world of modern manufacturing, the strategy of plastic extrusion plays an instrumental role. Unwinding the fundamentals of this process reveals the real convenience and potential of plastic extrusion.
The Fundamentals of Plastic Extrusion Process
While it might show up facility, the fundamentals of the plastic extrusion process are based upon relatively uncomplicated concepts. It is a manufacturing procedure in which plastic is thawed and after that shaped into a constant account via a die. The raw plastic product, typically in the type of pellets, is fed right into an extruder. Inside the extruder, the plastic undergoes warmth and stress, creating it to thaw. The liquified plastic is after that compelled via a designed opening, referred to as a die, to develop a long, constant product. The extruded product is cooled and then reduced to the desired size. The plastic extrusion procedure is thoroughly made use of in numerous sectors as a result of its cost-effectiveness, effectiveness, and flexibility.
Various Kinds Of Plastic Extrusion Strategies
Building upon the standard understanding of the plastic extrusion process, it is needed to check out the numerous methods associated with this manufacturing approach. Both main strategies are profile extrusion and sheet extrusion. In account extrusion, plastic is melted and created into a continuous account, typically made use of to create pipes, poles, rails, and window frameworks. In contrast, sheet extrusion develops huge, level sheets of plastic, which are commonly more refined right into items such as food packaging, shower drapes, and vehicle parts. Each method calls for specialized equipment and precise control over temperature and pressure to make sure the plastic keeps its form during air conditioning. Recognizing these techniques is essential to using plastic extrusion properly in modern manufacturing.

The Function of Plastic Extrusion in the Automotive Market
An overwhelming bulk of parts in modern vehicles are items of the plastic extrusion process. This procedure has transformed the automotive sector, transforming it into an extra effective, cost-efficient, and versatile production market. Plastic extrusion is mainly made use of in the production of various auto elements such as bumpers, grills, door panels, and control panel trim. The process provides an attire, constant output, making it possible for suppliers to generate high-volume components with excellent accuracy and marginal waste. The agility of the extruded plastic components adds to the total decrease in vehicle weight, boosting fuel performance. Additionally, the sturdiness and resistance of Learn More Here these components to heat, cool, and influence enhance the long life of automobiles. Thus, plastic extrusion plays an essential role in auto manufacturing.

Applications of Plastic Extrusion in Customer Product Production
Past its substantial effect on the vehicle market, plastic extrusion verifies equally effective in the realm of consumer products making. The adaptability of plastic extrusion enables manufacturers to develop and generate complicated shapes and dimensions with high precision and performance. The versatility, adaptability, and cost-effectiveness of plastic extrusion make it a favored selection for numerous consumer items manufacturers, contributing significantly to the market's development and innovation.
Environmental Effect and Sustainability in Plastic Extrusion
The prevalent use of plastic extrusion in manufacturing invites examination of its ecological ramifications. As a procedure that frequently utilizes non-biodegradable products, the environmental impact can be substantial. Energy intake, waste production, and carbon emissions are all concerns. Nonetheless, market innovations are raising sustainability. Efficient machinery decreases energy use, while waste administration systems recycle scrap plastic, reducing raw product needs. In addition, the development of biodegradable plastics uses a much more ecologically pleasant option. In spite of these improvements, even more advancement is required to reduce the environmental footprint of plastic extrusion. As society leans towards sustainability, makers need to adjust to remain viable, emphasizing the importance of continuous study and innovation in this area.
Final thought
In final thought, plastic extrusion plays an important function in modern production, particularly in the automobile and customer products great site sectors. Its adaptability permits the manufacturing of a broad variety of parts with high precision. Its possibility for recycling and advancement of biodegradable materials offers a promising method towards lasting practices, thereby attending to environmental issues. Comprehending the fundamentals of this procedure is key to maximizing its applications and advantages.
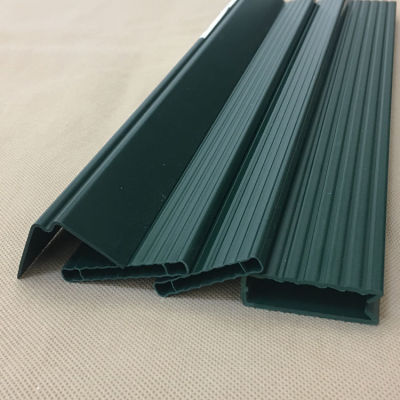
The plastic extrusion process is extensively used in numerous sectors due to its cost-effectiveness, efficiency, and versatility.
Building upon the standard understanding of the plastic see post extrusion process, it is necessary to discover the different techniques involved in this manufacturing approach. plastic extrusion. In contrast, sheet extrusion produces big, flat sheets of plastic, which are typically additional refined right into items such as food product packaging, shower curtains, and car components.A frustrating bulk of components in modern automobiles are products of the plastic extrusion process